The Future of Denim with Saitex
In the making of our men’s
jeans, we’ve partnered with an
industry-leading manufacturer
that’s revolutionising the way
denim is made.
Located in Vietnam, Saitex is a denim manufacturer focused on supporting environmental and social change. The factory is driving innovation at key stages of denim production to address energy use, water consumption and waste. From spinning the raw cotton fibre to weaving the denim and constructing the garment, every step of production is completed in-house at Saitex.
Discover some of the ways Saitex is changing the fabric of the denim industry.
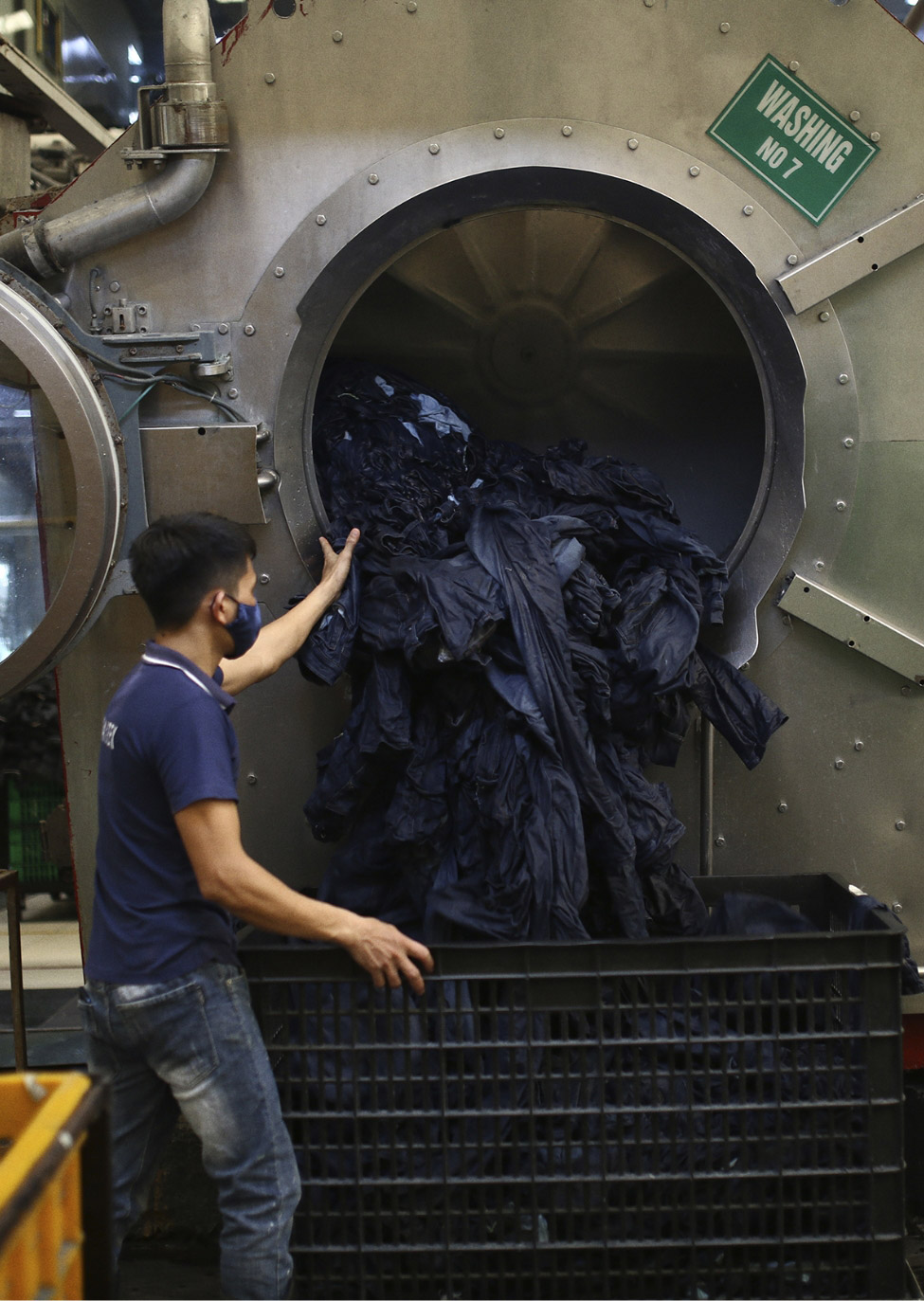
Energy solutions
In a commitment to conserving energy, Saitex has 9,500 solar panels on the roof of its mill that help to power the facility. In addition, the sewing factory is Silver LEED (Leadership in Energy and Environmental Design) certified, an internationally recognised symbol of sustainability excellence and green building leadership. Buildings that are LEED-certified are designed to reduce carbon emissions, energy, water and waste.
The smart system behind
the dyeing process
To achieve the rich tones of our jeans, Saitex draws on the innovative dyeing technology of Smart-Indigo™, and was one of the first denim manufacturers to invest in a Smart-Indigo™ machine. According to Smart-Indigo™, its system reduces carbon dioxide emissions, as well as energy and harmful chemical use.
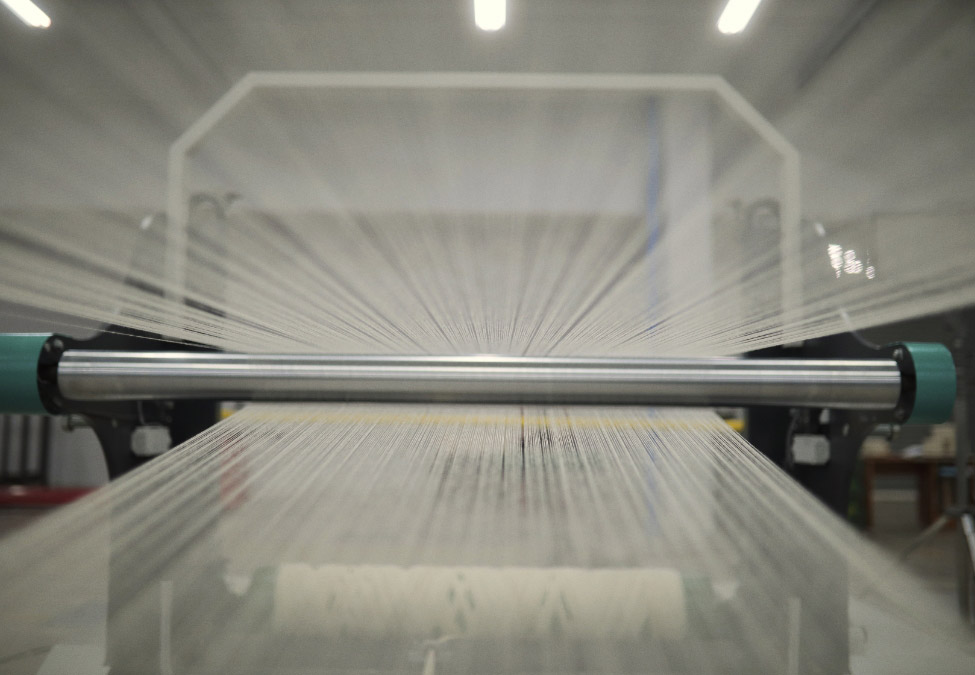
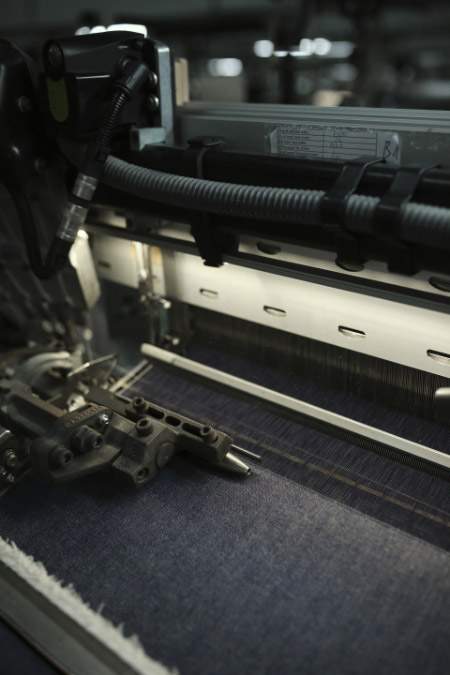
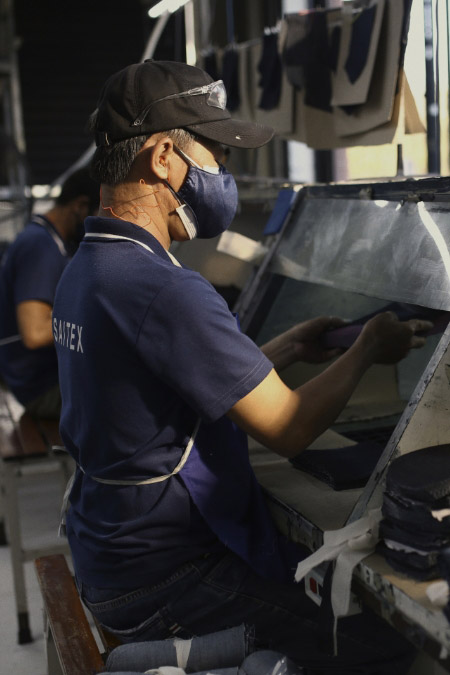
From wastewater to
a valuable resource
At Saitex, denim is washed using a closed-loop system that recycles approximately 98% of water through an on-site treatment plant. By recycling water in-house, Saitex is able to reduce the need for fresh water in the washing process.
Working to reduce chemical use
Saitex was the first denim laundry in the world to become a bluesign® system partner. The globally recognised bluesign® system assesses facilities to reduce harmful substances and carbon dioxide emissions in the textile industry, while improving water and energy consumption.
Taking drying back to basics
Rather than solely relying on traditional tumble drying, Saitex air dries its jeans for up to 80% of the drying process. Jeans are hung from the ceiling of the wash facility to conserve energy while drying, a process which can take up to three hours for each pair.
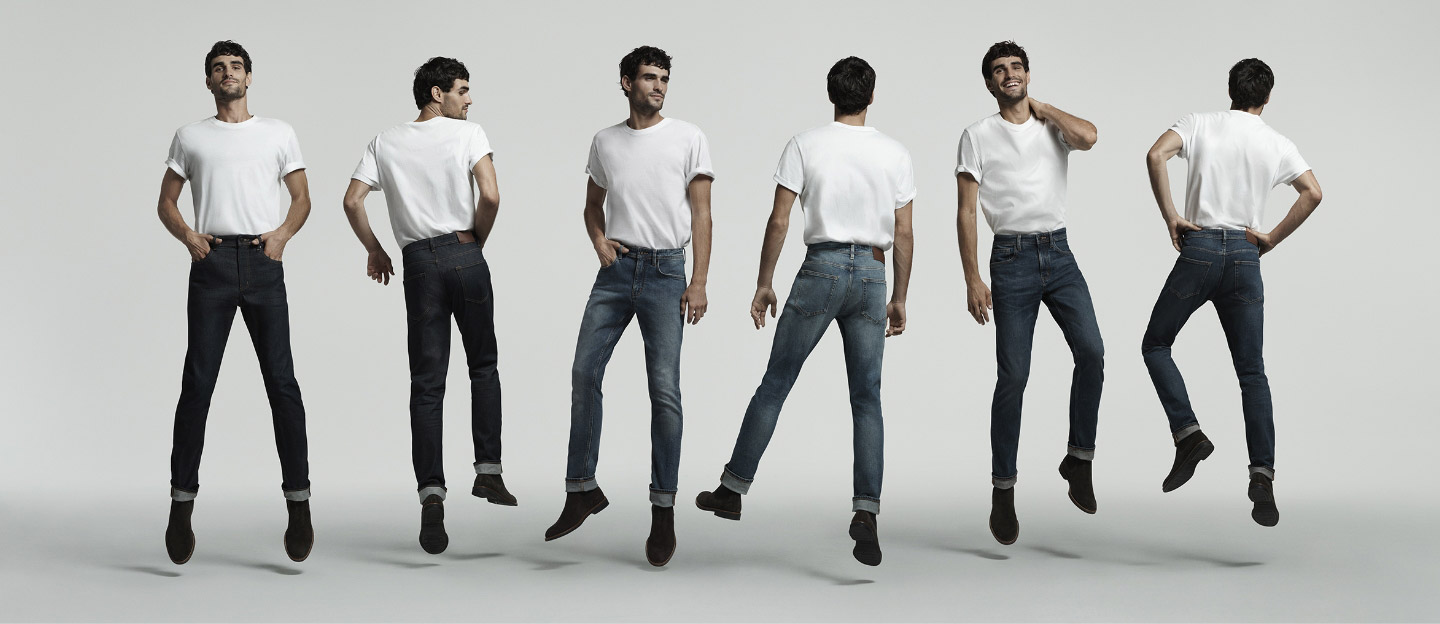
Our denim jean
We’ve worked hard to perfect our men’s jean, from the heavier fabric weight to the indigo colour that lends a richness of tone to every pair. The cotton is sourced from farms that aim to increase soil health, encourage biodiversity and improve water management.
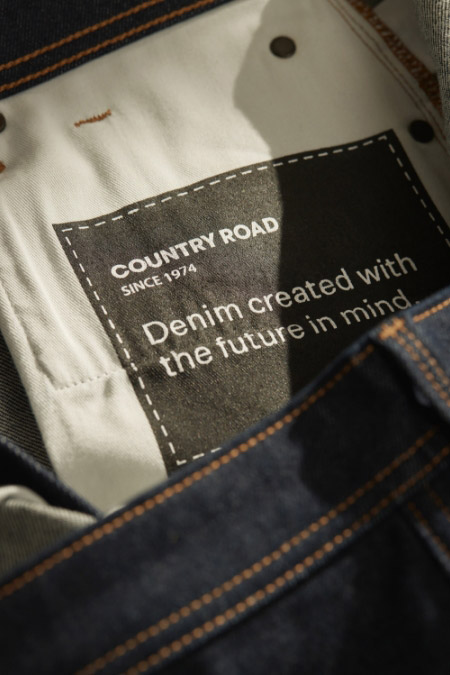
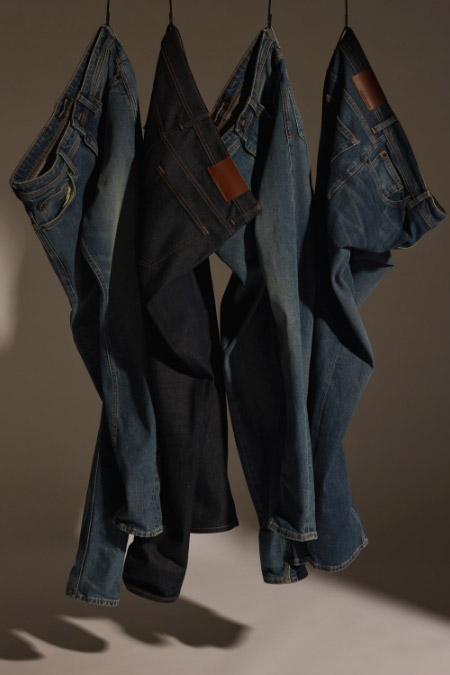
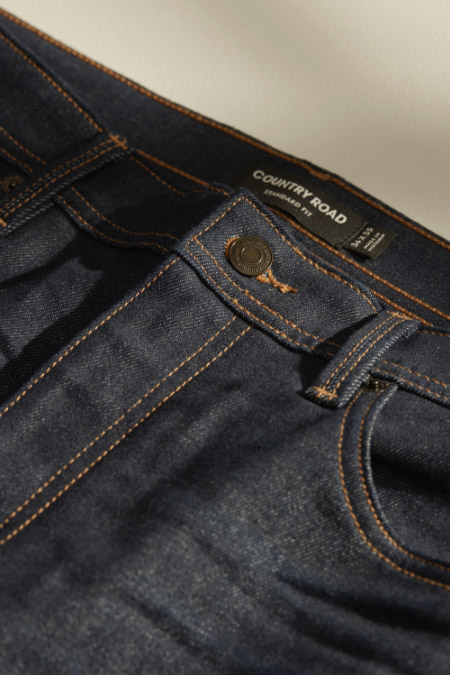
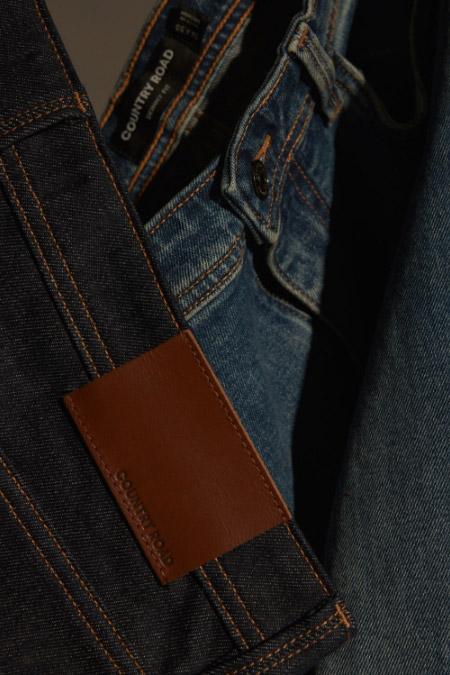
Creating pathways into
the fashion industry
REKUT is a program run by Saitex that offers training and employment for marginalised groups and people with disability. The training program helps to create pathways into the fashion industry with participants given the opportunity to progress into permanent positions on Saitex’s sewing lines.
Turning textile waste
into beautiful homewares
Recognising the value of fabric waste, Saitex has repurposed denim off-cuts and seconds to create a new material. Stelapop© is a wood alternative that is made using 65% recycled denim sourced from Saitex.
Stelapop can be used to create homewares, furniture, and other items that would normally be made from wood or plastic. Unlike these materials, though, Stelapop contains flecks of textile and variance in colour that add character, and it can be recycled once it is no longer in use, creating a fully circular system.
In partnership with Stelapop, we’ve worked to create serving pieces from this innovative material that embraces future possibilities while showcasing its origins.

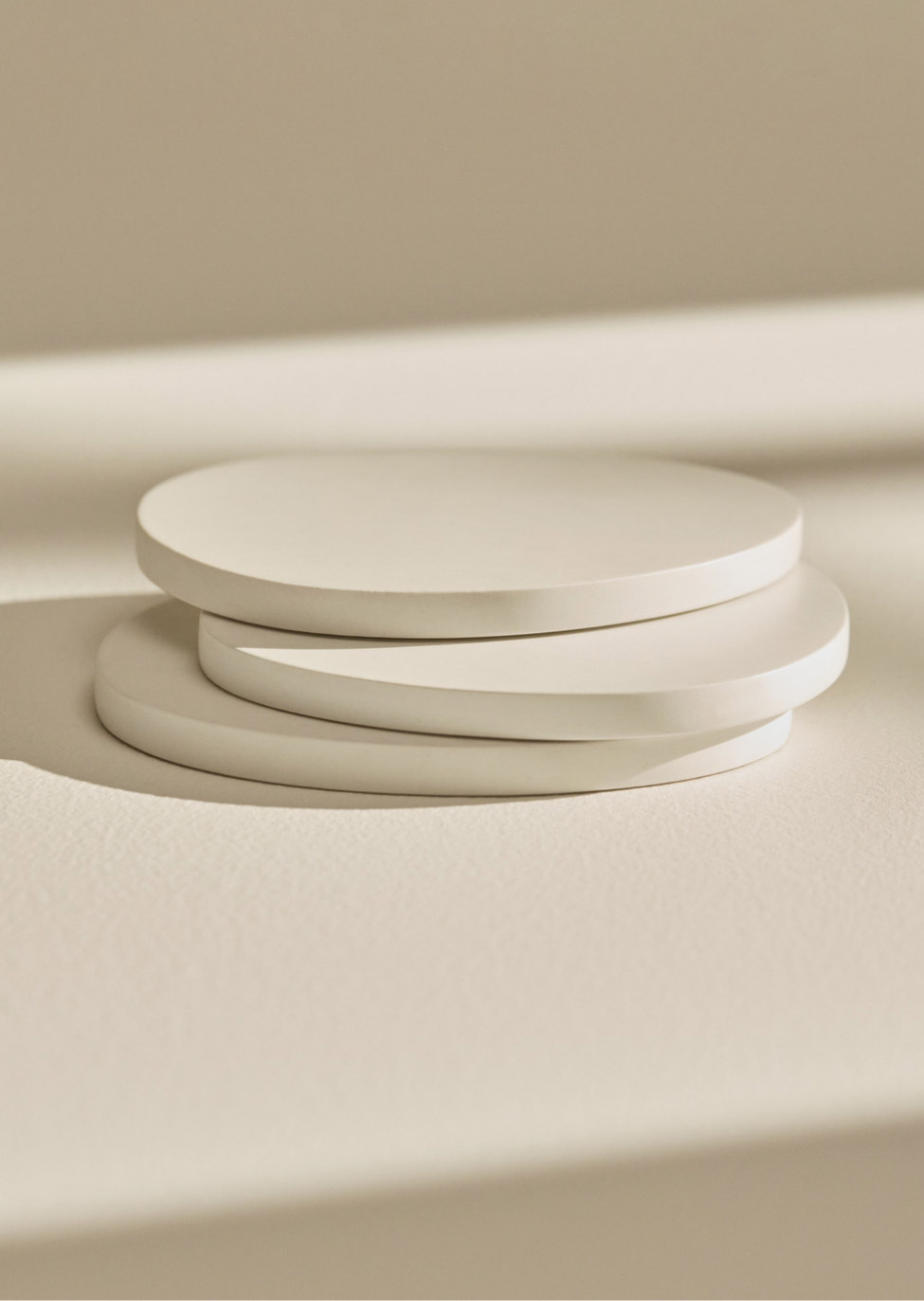
Shop the story